Design for Manufacturing vs. Traditional Product Design: Key Differences
Understanding Design for Manufacturing (DFM)
Design for Manufacturing, often abbreviated as DFM, is a design approach that focuses on designing products with the ease of manufacturing in mind. The primary goal of DFM is to simplify the manufacturing process, reduce costs, and improve product quality. By incorporating manufacturing considerations at the design stage, companies can streamline production and minimize potential issues that could arise during manufacturing.
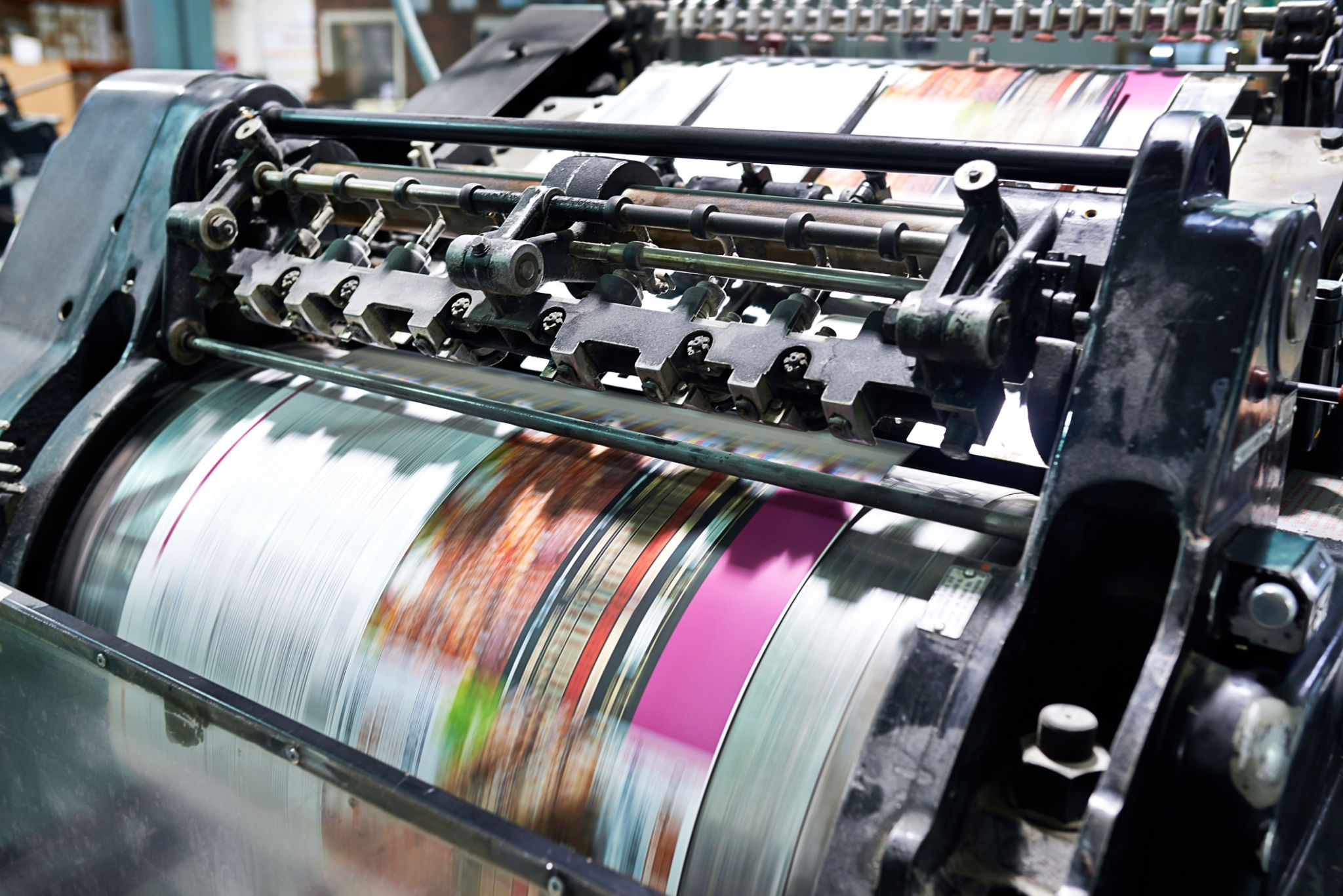
Key Principles of DFM
DFM involves several key principles that guide the design process. These principles include:
- Standardization: Using standard components and processes to facilitate easier assembly and reduce costs.
- Minimization: Reducing the number of parts in a product to simplify assembly and reduce potential failure points.
- Tolerance Design: Designing parts with appropriate tolerances to ensure manufacturability and functionality.
Traditional Product Design Overview
In contrast, traditional product design emphasizes aesthetics and functionality without heavily considering the manufacturing process. This approach often results in innovative and unique products but can lead to challenges when moving to production. Traditional design focuses on the final product's performance and market appeal, sometimes at the expense of manufacturability.
Characteristics of Traditional Design
Traditional product design is characterized by:
- Creative Freedom: Designers have more flexibility to explore unique forms and features.
- Focus on End-User Experience: Emphasis is placed on how the product will be used and perceived by consumers.
- Aesthetic Innovation: Often results in visually striking products that stand out in the market.

Comparing DFM and Traditional Design
When comparing DFM and traditional product design, the most significant difference lies in their approach to the manufacturing process. DFM prioritizes practical considerations, while traditional design often prioritizes creativity and user experience. Let's explore some key differences:
Cost Implications
One of the most critical differences between DFM and traditional design is their impact on production costs. With DFM, cost efficiency is a primary objective. By streamlining production methods and minimizing complexity, DFM can lead to lower manufacturing costs. Traditional design, however, may result in higher costs due to more complex designs and specialized materials.
Time to Market
The time required to bring a product to market can also vary significantly between these two approaches. DFM typically results in a faster time to market due to its focus on manufacturability from the outset. Traditional design may require more iterations and redesigns during the production phase, potentially delaying product launches.
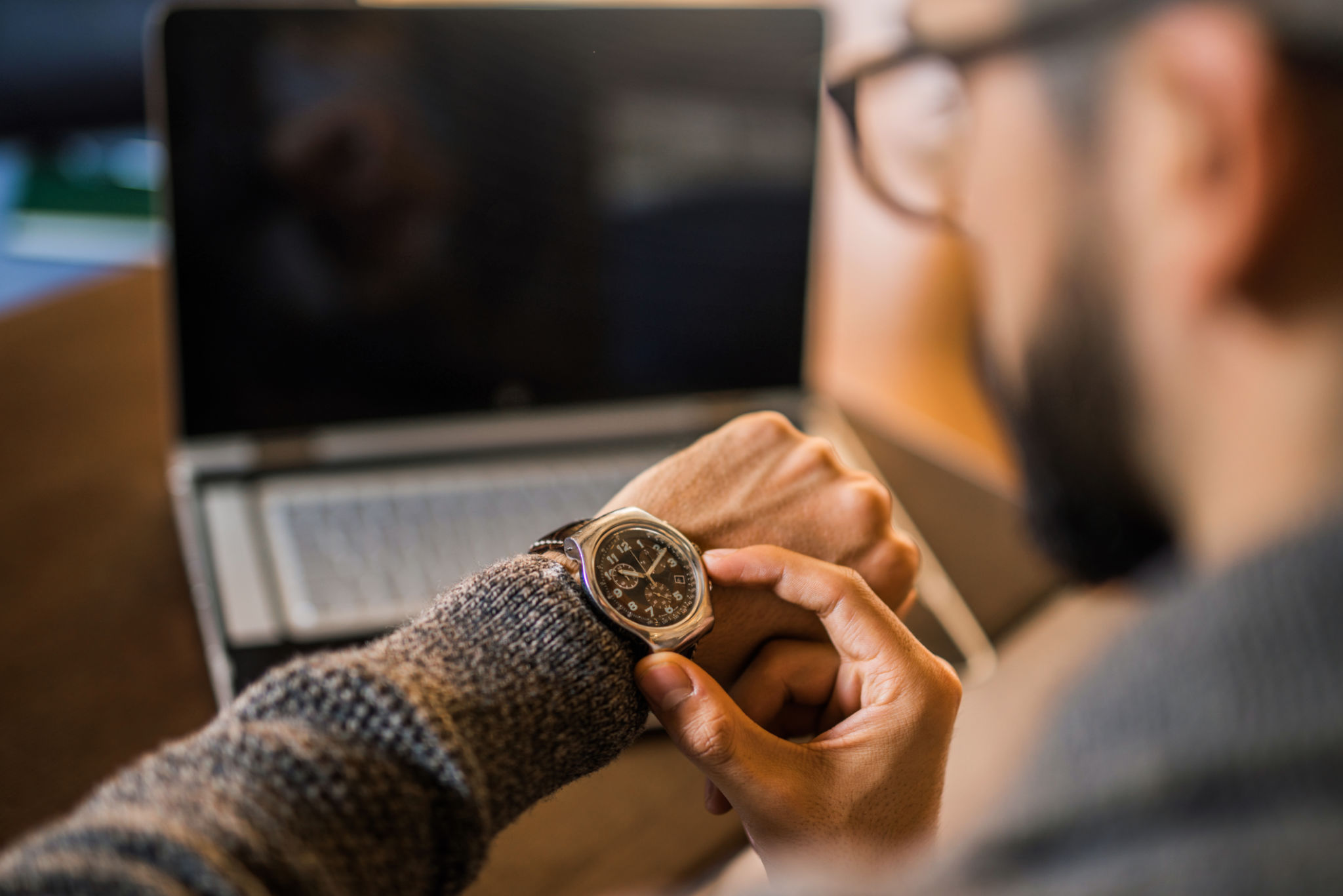
Choosing the Right Approach
The decision between using DFM or traditional design largely depends on a company's specific goals and resources. For businesses aiming for efficiency and cost savings, DFM is often the preferred choice. However, for companies looking to push creative boundaries and deliver innovative products, traditional design might be more suitable.
Ultimately, some companies find success by blending both approaches. By integrating manufacturability considerations into the creative process, businesses can achieve a balance between innovation and practicality. This hybrid approach allows for the creation of products that are both groundbreaking and efficiently produced.